- PRODUCTS
-
- CNC Metal Cutting Equipment
- Cylinder Processing Equipment
- Round Bar Peeling Machine
- Straightening Machine
- Chip Handling Equipment
- Polishing Machine
- Surface Grinder
- Electroplating Equipment
- Drawing Machine
- CNC Machining Center
- Center-less Grinding Machine
- Production Line
- Cylinder Processing
- Rolling Mill
- Free Forging Machine
- Chamfering&Facing Machine
- Heat Treatment Machine
- Vacuum pump
- Application
- Contacts Us
-
Mobile +8618663896299
-
Fax +86-535-6896668
-
E-mail: haige@haigechina.com
Skiving & Roller Burnishing Machine
Detailed Introduction
It has the following advantages compared with traditional honing:
1)Improve processing efficiency: Processing speed is nearly 20 times that of honing.
2)Enhance surface hardness: Surface hardness is increased by more than 50%.
3)Processing precision: Processing precision can reach level IT8, and surface roughness can reach Ra0.05-0.4μm.
4)Working environment: Low noise, non-pollution, labor cost-saving.
5)Reasonable processing arrangement: Skiving & roller burnishing can be arranged as the last operation after the others (such as drilling oil filler hole, welding, threading).
Headstock: Ensure large torque at low speed and constant power output at high speed by adopting ZF gear two-speed transmission box made in Germany. Imported precision bearing is adopted for the main shaft, to ensure its stiffness and precision.
Boring bar support base: With a new internal structure, it can eliminate vibration effectively when the boring bar is revolving, and ensure the minimization of cutter deviation.
Clamping base: clamp male cone of the work piece by moving the hydraulic cylinder against the locating base, to have the work piece fixed. It is easy and convenient to install and replace the locating base.
Locating base: a new locating base locking device is adopted to fix the locating base at the desired place.
Work piece supports: there are two work piece supports. With a V structure, each of them can be adjusted freely according to outer diameter center of the work piece. For they are installed on the guide rail slide, it is convenient and easy to push them.
Chip conveyor and filtering system: with a chip-removing method combining chain type chip conveyor with comb separator, the filtering precision can be ensured through multistage filtration and high-precision filtration by suction filter.
Cooling system: the bed cavity is used as the fuel tank body, thus saving the floor area required, and providing cooling oil with different pressures and flow rates for processing work pieces with different diameters. The filtering precision can be ensured through ten-stage filtration and high-precision filtration by suction filter.
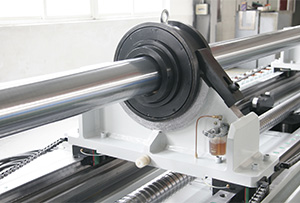
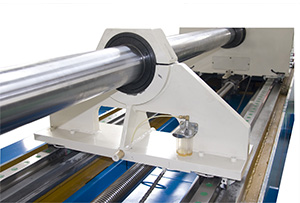
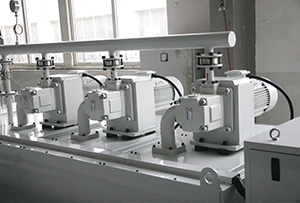
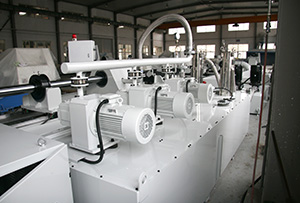
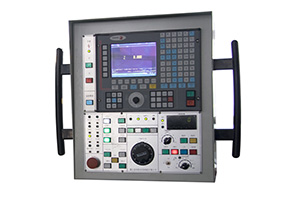
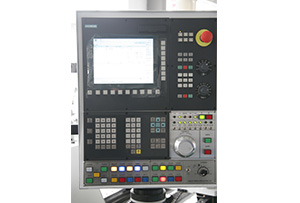
Technical Parameter
Main Technical Parameters | |||||
Machine tool model | ZTG2530 | ZTG2560 | ZTG2590 | ZTG1830 | |
Workpiece size | Inner diameter (mm) | 50-250 | 80-250 | 90-250 | 50-180 |
Outer diameter (mm) | 60-300 | 90-300 | 100-300 | 60-250 | |
Processing length (mm) | 500-3000 | 1200-6000 | 1650-9000 | 500-3000 | |
Speed | Spindle speed (r/min) | 50-1500 | |||
Positioning seat movement (mm/min) | 6000 | ||||
Spindle box movement (mm/min) | 8000 | ||||
Motor power | Spindle servo (Kw) | 37/56 | |||
Feed servo (Kw) | 6 | ||||
Cooling system | Fuel tank capacity (L) | 4150+1850 | 4150+1850 | 6000+1850 | 4150+1850 |
Pump flow rate (L/min) | ≥500 | ≥500 | ≥700 | ≥500 | |
Filtering accuracy (μm) | 50 | ||||
Total motor power (Kw) | 90 | 90 | 100 | 85 | |
Machine tool dimensions (mm) | 11000x3600x2200 | 18820x3600x2200 | 25400x3600x2200 | 11000x3600x2200 | |
CNC system | FAGOR、SIEMENS | ||||
Note: Our company can provide CNC scraping and rolling machines with different configurations such as 1m, 1.5m, 2m, 3m, 6m, 9m, etc. It can also be customized according to the special requirements of customers |